Largely due to all the disruption in the global supply chain tied to the pandemic, we have been seeing a lot of inconsistent sealing results. As manufacturers are forced to try new products or accept replacement products, they are experiencing both incompatibility and quality issues with caps, containers, and liners.
We recently brought together some industry experts to discuss the sealing industry’s current state and help businesses address some of the challenges they may be facing. Joining the discussion were Jessica Toellner, Regional Sales Manager from Enercon Industries, Jeff LaGrange, Cap Sealing Product Line Manager from Enercon Industries, and Owen Schmidt, Account Executive from MJS Packaging.
Throughout this article, we will discuss how you can identify what a “good seal” looks like when there are no set industry standards, different ways to test your seals, and some of the common causes of seal failures.
Induction Sealing
When it comes to product packaging, induction seals are crucial. Induction sealing is the process of forming a hermetic seal using a heat-seal foil cover over a closure that is lined with an induction sealing material. The hermetic seal guarantees that the contents are airtight, preventing any contaminants from entering.
Induction seals are used to ensure the safety of products such as pharmaceuticals, food and beverages, and cosmetics. Induction seals give consumers another level of protection in assuring that a product is unaltered from when it was originally sealed.
Induction Sealing Process
Induction sealing is a non-contact process. There is no human contact in the in-line sealing process to reduce the chance of human error. The induction process uses equipment that creates an induction field that heats up the layer of foil in the liner and activates the sealing layer on the bottom of the liner, resulting in a hermetic seal.
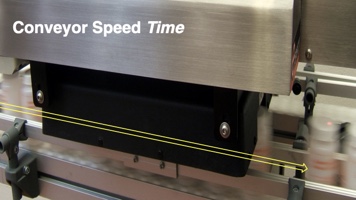
There are three main principles to induction sealing: pressure, heat, and time.
Pressure
Pressure is the most important part of ensuring a proper seal. This is done through the cap application torque and the lid flatness. The positive pressure from the inside of the cap is offset by a greater downward force to ensure that there is enough torque to form a good seal.
Heat
The heat comes from the reaction of the electromagnetic field and foil heat. The amount of heat will vary depending on the type of sealing head that is being used.
Time
The time means the speed of the conveyor speed. The conveyor speed is primarily focusing on the dwell time, which is how long each bottle will spend going through the sealing process.
What Causes Induction Sealing Failures?
The most common cause of induction sealing failures is insufficient application torque. One of the most important aspects of sealing operations is to ensure you are measuring your cap torque. A recommended guideline is to use about 1/2 of the cap’s size in inch/lb in terms of application torque.
Caps can loosen during the induction sealing process. Do you need to retorque? No, not necessarily from a sealing perspective. If the cap was tight enough going into the machine, it should be fine.
With supply chain issues being worldwide, liner issues are increasing as well. Many of our customers have been forced to use alternative liners as lead times have increased significantly. While lead times used to average around 10 days, we are now typically seeing 6-7 months. When utilizing an alternative liner, it is crucial to qualify and test the liner to ensure success.
Liner Compatibility
Something that is very important in ensuring a proper seal is understanding the compatibility of the product with the liner. If you are dealing with a very oily or grease-related substance or an aggressive product, selecting the proper liner is essential for sealing success. When dealing with challenging substances, we often add a barrier layer to further protect the product. This protects the foil from the product.
Storing Liners
Storing liners can play a significant role in the success of the seal. One of the most important elements of the storage is to ensure that heat and humidity levels are controlled.
For example, if you have a container with a liner that has moisture absorbed in the material and you store it at high heat and humidity for an extended period of time, there will likely be some swelling as this moisture is released from the polyolefin polymer. This will hinder the seal integrity and ultimately create issues downstream during your run.
Container Compatibility
Similar to the liner compatibility, the container must be specifically chosen for each use case. The heat seal polymer of the liner must be compatible with the container to ensure there is proper bonding during the sealing process.
There are universal liners available for nearly every container size, but the best option is to test out your seal. While these liners claim to be universal, there are some inconsistencies with these liners, especially with the longevity of the seal quality. These liners, while extremely versatile, also have very low chemical resistance and are not suitable for many product formulations.
With so many variables in play in our industry today, it is always better to ensure proper testing is completed prior to production.
Cap Issues
Cap issues are also a common challenge when dealing with liners. When you are selecting your cap, it is important to consider the compatibility of the cap and its liner with the container.
One of the largest cap issues is thread alignment. Thread alignment issues typically arise when the cap liner is not properly indexed. This can be caused by a number of things, including substrate construction or even incorrect installation of the liner.
It is crucial to ensure your supplier has the proper equipment to index their lids and seals per packer specifications to reduce thread alignment issues during sealing.
By understanding how these components work together, you’ll have a better chance at identifying problems before they occur on the product line.
Container Issues
Land area is essential in determining the quality of the seal. You must ensure the land area is wide enough for the liner/container contact.
Having a smooth, flat surface is also important for proper seal performance. If the container is not smooth or has high sealing surface variations, chances are you will have some issues with your seals.
Test frequency needs to be determined based on how often you change out containers used in production. The same goes with the liner, as different substrates may require more frequent testing than others.
Operating Windows
An operating window is used to define the proper operating conditions for your equipment to allow your seals to perform at their best.
This window typically includes material, process, and environmental parameters that should be considered. If any of these items are off slightly, you will see some issues with production. Setting up an operating window is an important step in ensuring your success because there are variables that will come into play during the sealing process that must be accounted for. These variables include cap torque, container centering, line speed, and foil height.
Operating Conditions
In order to run an operating window, the proper conditions must be set. For best results, run tests using full containers, at temperature, using the actual line speed, and make sure you successfully seal 2 dozen containers throughout the test.
How to Set Up Your Operating Window
The purpose of this test is to find the range where you will get the best seal quality. You must have a proper setup of your sealer. The general number that we use to give you the best performance is a 1/8 inch air gap between the bottle and the coil. This air gap needs to be level all the way across the seal head. To do this, you must use a gap gauge for consistency.
You also must have a controlled and centered bottle path. This ensures you have even heating levels before the ceiling window test can begin.
Testing Plan
Here are the recommended steps for creating your operating window test.
- Determine your minimum set-point. Start below the anticipated power output. This is a gradual scaling process. You begin with 1 bottle at a low power output. If that does not seal, then you increase the power output by a small margin. Put another bottle through the conveyor. If this does not seal, then continue to increase the power until you find the output needed for a high-quality seal.
- Find the maximum set-point. Repeat the process in step 1, but try to find the maximum output for a high-quality seal. This process will allow you to find the median point for a good seal level.
Summary
- Having a proper seal is essential in the production process.
- Having a good container and lid combination will also improve seal quality and ultimately the success of the product.
- Make sure you test your conveyor process and find the optimum output to account for variability in the sealing process.
MJS Packaging can always assist and guide you in determining the best packaging and seal option for your products. Contact us today to speak with one of our team members.